
The circuit is made with 4 NPN transistors (I used.
FORWARD AND REVERSE MOTOR DRIVER
This means that if the coil that drives the motor in the forward direction is energized, a normally closed set of contacts wired in series with the reverse coils will prevent that coil from being energized as long as the forward coil remains energized.Get Images Library Photos and Pictures. STK681-332GEVB, Brand ON Semiconductor, Power Management Function, Kit Name Current Control Forward/Reverse DC Motor Driver Evaluation Board, Featured Device STK681-332-E. In this video we create a single circuit called an H-Bridge to allow bi-directional control of a DC motor. This is done to avoid dead short circuit in case both the contactors closing simultaneously. Similarly, moving the joystick to the left or right will increase or. When the joystick moves downward, the PWM value increases on pin D6 (and the motor speed accelerates in a reverse direction). The forward and reverse contactors are mechanically interlocked i.e., if one of them is closed the other cannot close. When the joystick moves upward, the PWM value gradually increases from 0 to 255 (0 100) on pin D5 (and the motor speed accelerates forward). To prevent unintentional energization of both the forward and reverse coil at the same time, the coils are equipped with normally closed contacts, which are then wired in series with the opposite direction’s coil to act as an electrical interlock. This can be accomplished by using two contactors, one for the forward or CW rotation and one for the reverse or CCW rotation. 12V 24V 36V 48V 40A Forward Reverse reversible DC Speed Motor Controller For Brush Motor Technical Parameters Operating voltage: DC10V-50V Output voltage: Load Linear Forward Reverse: YES Maximum current: 60A Continuous current: 40A Speed range: 0 - 100 Connection: Barrier Terminal Blocks PWM Frequency: 15KHZ Quiescent Current: 0. If you find that the up down positions of the switch makes the motor move in directions opposite to what you would prefer, simply re-orient the switch, or you can switch the wire connections to either the battery or motor terminals. If a motor is to be driven in two directions, then it will require a Forward / Reverse motor starter, which has two three-pole horsepower-rated contactors rather than just one as in the conventional starter. Reversal of three-phase motor rotationīoth coils power contacts feed through a single set of OLR to provide running protection in both directions. The up position should make the motor move forward, and the down position should make it move backward.
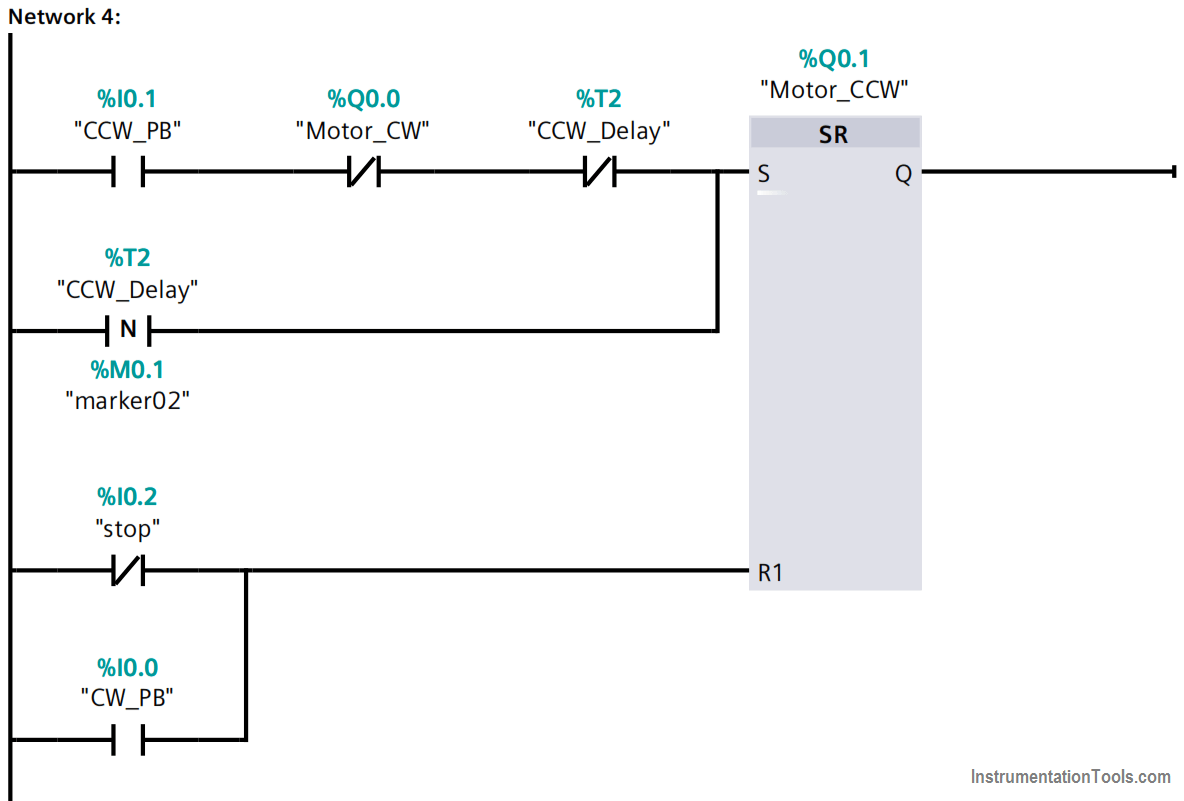
FORWARD AND REVERSE MOTOR HOW TO
The circuit diagram for dc motor forward reverse control with 2 push switches electric directions or actuator backward how to wire a work in reversing switch 3 phase ac wiring circuits ladder logic question wphmoto high sd 48v 1800w switching of single dpdt reversal. When the alternate coil is energized, Lines 1 and 3 are interchanged with Terminals 1 and 3, allowing for a phase shift in the 3-phase circuit, driving the motor and causing it to rotate in the opposite direction. DC motor speed controller Forward and Reverse make a dc motor forward & reverse conteoller use DPDT switch.shorts dcmotorforward reverse amazing mono. Explanation Of Forward And Reverse Circuit Diagram Motor Electronic Paper. PWM Motor Speed Controller 6V 9V 12V 24V 36V 48V 60V DC 6V - 30V Pulse Width Modulation Regulator 8A 180W Stepless Variable Speed Switch DC Speed Regulation (PWM 10A Forward Reverse) 4.0 out of 5 stars. They are connected so that under normal conditions, one coil will connect L1 with T1, L2 with T2, and 元 with T3. Motor Starters and Contactors 15 Forward/Reverse Starters NEMA Forward Reverse motor starter with OLRĪ forward/reverse magnetic motor starter is constructed from two regular contactors installed with a mechanical interlock that prevents both coils from pulling in simultaneously.
